Deburring
Allow us to remove sharp edges from your parts, enabling full focus on what truly matters.
Deburring Services :
What is Deburring Services ?
Deburring is the process of removing sharp edges from machined parts. Burrs are small, unwanted protrusions that can be left behind after machining. They can be sharp and can cause injury, so it is important to remove them.
Deburring is an important process in manufacturing. It helps to ensure that machined parts are safe and that they have a smooth finish. Deburring can also improve the performance of parts by removing sharp edges that can cause stress concentrations.
There are two main types of burrs: external burrs and internal burrs. External burrs are the most common type of burr. They are located on the outside of the part and can be caused by a variety of factors, such as the cutting tool, the feed rate, and the depth of the cut. Internal burrs are located on the inside of the part and are often caused by the drill bit or the reaming tool.
There are a number of different deburring standards available, such as the American National Standards Institute (ANSI) and the International Organization for Standardization (ISO). These standards provide guidelines for the deburring process, such as the size of the burrs that should be removed and the methods that should be used.

There are a number of different deburring methods, including :
- Manual Deburring: Hand tools like files, abrasive stones, sandpaper, or deburring knives are used to manually remove burrs. Although simple, it is time-consuming and may lack consistency.
- Mechanical Deburring: Various mechanical methods, including tumbling, brushing, and grinding, employ abrasive media to remove burrs from multiple parts simultaneously.
- Thermal Deburring: Also known as “burnishing,” this method uses a combination of oxygen and fuel to ignite burrs, which are then removed by high-pressure gas.
- Electrochemical Deburring (ECM): ECM uses electrical current to dissolve burrs selectively, making it suitable for complex and hard-to-reach areas.
- Electrolytic Deburring (EDM): EDM employs an electrode and an electrolyte solution to dissolve burrs through controlled electrical discharges.
- Cryogenic Deburring: This process uses liquid nitrogen to freeze burrs, making them brittle and easily removable by subsequent mechanical methods.
- Ultrasonic Deburring: Ultrasonic vibrations are used to break up and remove burrs from delicate or intricate parts.
- Abrasive Flow Machining (AFM): In AFM, a semi-solid abrasive media is forced through the workpiece, flowing through and removing burrs from internal passages and complex shapes.
The choice of deburring method depends on the type of part being deburred, the size of the burrs, and the desired finish.
Importance of Deburring :
- Enhanced Functionality: Deburring ensures that components fit together seamlessly, reducing friction and wear, leading to better functionality and longevity of the finished product.
- Safety: Eliminating sharp burrs prevents potential injuries to both workers during assembly and end-users during product use.
- Aesthetics: Deburring improves the appearance and finish of the parts, contributing to a higher-quality final product that appeals to customers.
- Tolerance and Precision: Removing burrs aids in maintaining specified tolerances and dimensional accuracy in precision engineering applications.
Deburring Equipment :
- Deburring Machines: These machines automate the deburring process, improving efficiency and consistency. They may be designed for specific deburring methods or versatile enough to accommodate multiple techniques.
- Tumbling Barrels: Tumbling machines use rotating barrels or drums to tumble parts with abrasive media, effectively removing burrs.
- Brushing Equipment: Deburring brushes, available in various materials and configurations, can be used manually or attached to machines for automated deburring.
- Blasting Cabinets: Abrasive blasting cabinets employ compressed air or other gases to propel abrasive media against parts to remove burrs.
- Electrochemical Deburring Machines: ECM machines use programmable parameters for precise and controlled burr removal.
- Electrolytic Deburring Machines: EDM machines allow for the accurate and repeatable deburring of complex shapes.
Future of Deburring :
1. Automation and Robotics
The future of deburring in CNC servicing will witness increased automation through the integration of robotics. Automated deburring systems will be equipped with advanced sensors and AI algorithms, allowing them to identify burrs and precisely apply the deburring tools without the need for manual intervention. This automation will lead to reduced cycle times, improved consistency, and a safer working environment.
2. AI-Driven Deburring Strategies
Artificial Intelligence (AI) will play a significant role in optimizing deburring strategies in CNC servicing. AI algorithms will analyze the workpiece’s geometry, material properties, and machining data to determine the most efficient deburring approach. This will lead to better burr removal while minimizing material waste and energy consumption.
3. In-Process Monitoring and Quality Control
Real-time monitoring and quality control will become integral to CNC deburring processes. Advanced sensors and vision systems will continuously assess the workpiece during machining, detecting burrs as they form. This data will be used to adjust machining parameters or trigger automated deburring actions, ensuring that parts meet stringent quality standards.
4. Non-Contact Deburring Technologies
Future deburring techniques will include non-contact methods such as laser deburring and ultrasonic deburring. These technologies will be particularly useful for delicate or intricate components, where physical contact may pose a risk of damage. Non-contact deburring will also enable access to hard-to-reach areas, ensuring comprehensive burr removal.
5. Customized Deburring Solutions
Manufacturers will have access to more customizable deburring solutions tailored to their specific CNC applications. Advanced deburring machines will be designed to handle different workpiece materials, shapes, and sizes, accommodating a wide range of industry needs.
6. Integration with CNC Machining Centers
The integration of deburring capabilities directly into CNC machining centers will become more prevalent. This seamless integration will eliminate the need for separate deburring operations, saving time and increasing overall productivity. The CNC machine will perform deburring as part of its automated workflow, leading to more efficient and streamlined manufacturing processes.
7. Industry 4.0 and Digitalization
The future of deburring in CNC servicing will be shaped by the principles of Industry 4.0 and digitalization. Smart factories will utilize data-driven insights to optimize deburring processes, predict maintenance needs, and ensure consistent quality throughout production.
8. Eco-Friendly Deburring Techniques
Environmental concerns will drive the development of eco-friendly deburring techniques. Manufacturers will focus on reducing the use of hazardous chemicals and optimizing energy consumption during the deburring process, contributing to sustainable manufacturing practices.
9. Training and Skilled Workforce
As technology advances, there will be a growing need for skilled technicians and engineers who can operate and maintain sophisticated CNC deburring systems. Training programs and educational initiatives will play a vital role in preparing the workforce for the future of deburring in CNC servicing.
The future of deburring in CNC servicing looks bright. New technologies and techniques are being developed that will make deburring more efficient, effective, and environmentally friendly. As the demand for high-quality parts increases, so too will the demand for effective deburring methods.
Here are some of the benefits of using deburring machines :
- Consistent Burr Removal: Ensures uniform and consistent burr removal across multiple parts, reducing defects and variations in final products.
- Increased Productivity: Automation leads to faster processing, reducing manual labor and cycle times, resulting in higher output and shorter lead times.
- Enhanced Safety: Eliminates the need for operators to handle parts directly, promoting a safer working environment and reducing the risk of injuries.
- Improved Quality Control: Advanced sensors and monitoring systems ensure precise burr removal, maintaining consistent quality throughout production.
- Cost Savings: Reduces labor expenses and minimizes material waste, contributing to long-term cost efficiency.
- Versatility: Handles a wide range of materials and component shapes, providing customized solutions for different manufacturing needs.
Complex Geometries: Accesses intricate and hard-to-reach areas for comprehensive burr removal in complex shapes.

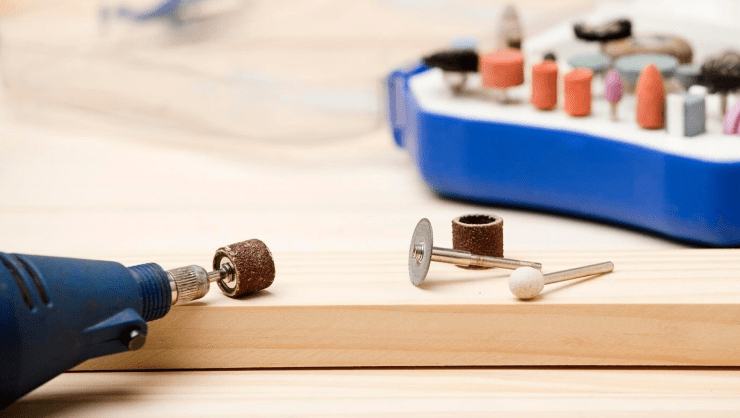
How Shivay Enterprise is different from other deburring service companies:
- Advanced Technology: Utilizes state-of-the-art deburring machines and equipment for efficient and precise burr removal.
- Specialization: Focuses exclusively on deburring services, developing specialized knowledge and expertise in the field.
- Customized Solutions: Offers tailored deburring services to meet individual client requirements.
- Quality Assurance: Implements rigorous inspection and monitoring methods to ensure high-quality, burr-free parts.
- Quick Turnaround Time: Delivers deburred components with reduced lead times, catering to clients with tight production schedules.
- Skilled Workforce: Employs experienced technicians well-versed in deburring techniques and equipment operation.
- Flexibility and Scalability: Can handle both small-scale and large-scale deburring projects, accommodating clients of varying sizes and industries.
- Continuous Improvement: Stays updated with the latest deburring technologies and industry trends for optimized services.
- Competitive Pricing: Offers cost-effective deburring solutions without compromising on quality.
- Excellent Customer Support: Prioritizes customer satisfaction and maintains clear communication with clients throughout the project lifecycle.
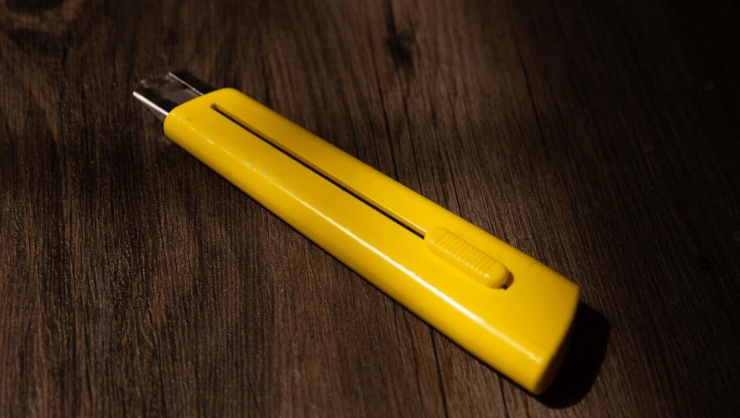

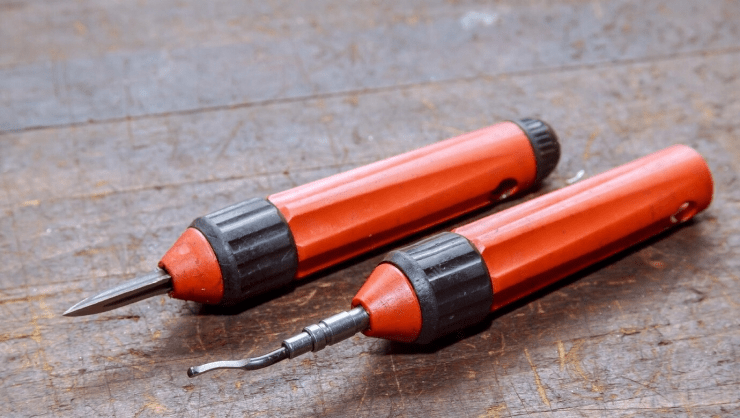
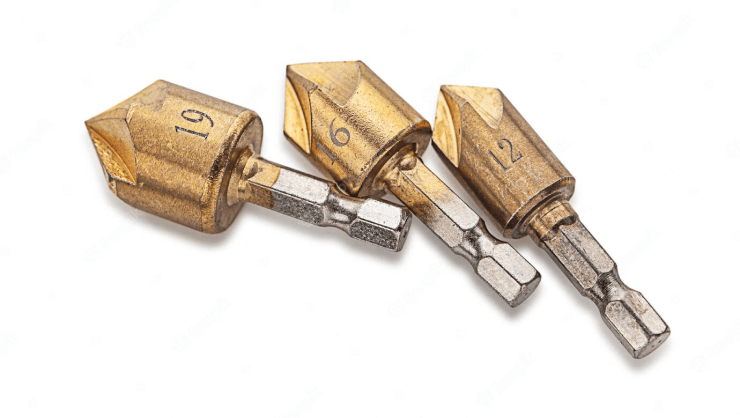
Deburring service is used in a wide variety of applications, including:
- Automotive Industry: Engine components, transmission parts, and precision parts for improved performance and assembly.
- Aerospace: Turbine blades, airfoils, and engine parts for precise tolerances and reliable operation.
- Electronics and Electrical Components: Electrical contacts, connectors, and semiconductor parts for enhanced conductivity and reliability.
- Medical Devices: Implants, surgical instruments, and medical equipment to prevent tissue damage and infection risks.
- Precision Engineering: Machinery, tools, and equipment for accuracy and functionality.
- Plumbing and Piping: Preventing leaks and ensuring proper fit in plumbing systems.
- Renewable Energy: Wind turbine components, solar panels, and renewable energy systems.
- Firearms and Defense: Weapon components for consistent performance and reliability.
- Marine and Shipbuilding: Critical parts for corrosion resistance and structural integrity.
- Railway Industry: Rails, fasteners, and rolling stock for smooth operation and reduced wear.
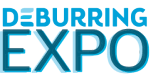
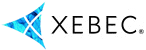

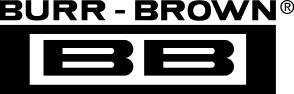

How Shivay Enterprise can help you with Deburring maintenance servicing:
- Expertise and Specialization: Specialized deburring service provider with extensive knowledge and experience in deburring techniques.
- Advanced Technology: Utilizes state-of-the-art deburring machines and equipment for precise and consistent results.
- Comprehensive Maintenance Solutions: Offers customized maintenance plans to suit your specific applications and production schedule.
- Quality Assurance: Thoroughly inspects and maintains deburring equipment to ensure efficient and reliable performance.
- Scheduled Maintenance Plans: Provides regular and scheduled maintenance to prevent breakdowns and reduce downtime.
- Quick Response and Support: Offers prompt response and support in case of issues or emergencies, minimizing disruptions to production.
- Performance Optimization: Fine-tunes and optimizes deburring equipment for improved efficiency and accuracy.
- Cost-Effectiveness: Professional maintenance services help save on repair expenses and increase equipment lifespan.
- Proactive Maintenance Approach: Identifies potential issues early on to prevent critical failures and ensure continuous operation.
- Industry Compliance: Ensures deburring equipment complies with industry standards and safety regulations.
- We can help you identify the types of burrs that are occurring on your parts. We can use our experience and expertise to identify the different types of burrs that are occurring on your part. This will help you to understand the cause of the burrs and how to prevent them from occurring in the future.
- We can help you develop a deburring plan that is specific to your needs. We can work with you to develop a deburring plan that is specific to your needs. This plan will take into account the size, complexity, and material of your parts, as well as the desired level of finish.
- We can provide you with deburring services. We can provide you with deburring services using a variety of methods, including CNC machines, wire brushing machines, and ultrasonic deburring machines. We can deburr parts quickly and accurately, regardless of the size or complexity of the part.
- We can train your employees on deburring techniques. We can train your employees on deburring techniques. This training will help your employees to understand the importance of deburring and how to deburr parts effectively.
Deburring in Aerospace
Deburring is the process of removing burrs, which are small, sharp edges that can be left behind after machining. Burrs can be a safety hazard, as they can cause cuts and injuries. They can also damage products, as they can create weak points that can lead to breakage.
Aerospace castings, such as engine blocks and turbine housings, must be free of burrs and other sharp edges to prevent them from causing damage to the casting or injury to workers. Deburring is a critical step in the finishing of aerospace castings to ensure their safety.


Deburring in Aircraft
Deburring is the process of removing burrs, which are small, sharp edges that can be left behind after machining. Burrs can be a safety hazard, as they can cause cuts and injuries. They can also damage products, as they can create weak points that can lead to breakage.
The best deburring method for a particular application will depend on the type of material being deburred, the size and shape of the part, and the desired level of finish.
Deburring is an important part of the manufacturing process in the aviation industry. By removing burrs, manufacturers can help to ensure the safety of their products and the safety of their employees.
Deburring in Energy
Deburring is the process of removing burrs, which are small, sharp edges that can be left behind after machining. Burrs can be a safety hazard, as they can cause cuts and injuries. They can also damage products, as they can create weak points that can lead to breakage.
The best deburring method for a particular application will depend on the type of material being deburred, the size and shape of the part, and the desired level of finish.
Deburring is an important part of the manufacturing process in the energy industry. By removing burrs, manufacturers can help to ensure the safety of their products and the safety of their employees.


Deburring in Pharmaceutical
Deburring is the process of removing burrs, which are small, sharp edges that can be left behind after machining. Burrs can be a safety hazard, as they can cause cuts and injuries. They can also damage products, as they can create weak points that can lead to breakage.
The best deburring method for a particular application will depend on the type of material being deburred, the size and shape of the part, and the desired level of finish.
Deburring is an important part of the manufacturing process in the pharmaceutical industry. By removing burrs, manufacturers can help to ensure the safety of their products and the safety of their employees.