Injection Molding
Unlocking Infinite Possibilities: Experience the Art of Precision Injection Molding with Our Trusted and Innovative Partner
Injection Molding Services
Injection Molding Casting ?
Injection molding is one of the most widely used and versatile manufacturing processes for producing plastic and polymer-based products. It involves injecting molten material into a mold cavity under high pressure and allowing it to cool and solidify to take the shape of the mold.
This process offers exceptional precision, efficiency, and repeatability, making it suitable for producing intricate and complex parts in large volumes. From consumer goods to automotive components, medical devices, and electronics, injection molding plays a critical role in various industries.
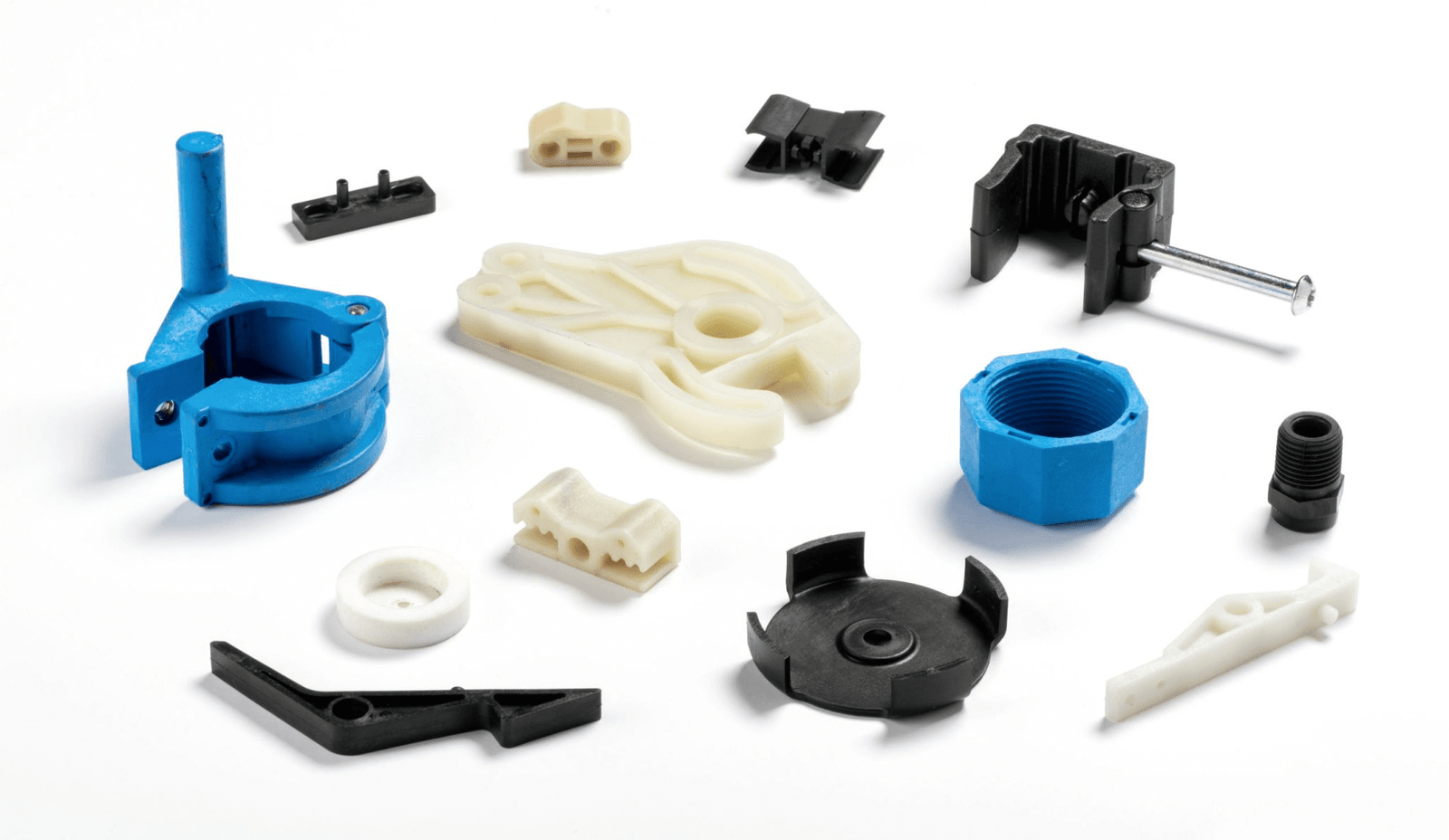
In this comprehensive guide, we will delve into the injection molding process, its types, materials used, equipment, applications, advantages, challenges, and the future of this essential manufacturing technique.
The Injection Molding Process :
- Clamping: The two halves of the mold, the stationary half (the “A” side) and the movable half (the “B” side), are brought together under high pressure. This forms a closed mold cavity.
- Injection: Plastic pellets or granules are fed into the hopper of the injection molding machine. They are heated and melted in the barrel, and the molten plastic is forced into the mold cavity through a nozzle and sprue.
- Cooling and Solidification: The molten plastic cools and solidifies inside the mold cavity, taking the shape of the mold.
- Ejection: Once the plastic has solidified, the mold opens, and the part is ejected using ejector pins.
- Post-Processing: The ejected part may undergo additional post-processing, such as trimming, assembly, and surface finishing, depending on the specific requirements.
Types of Injection Molding :
- Conventional Injection Molding: The standard injection molding process, as described above, is suitable for a wide range of plastic products.
- Micro Injection Molding: Specialized for producing tiny, precise components, often used in medical devices and electronics.
- Multi-Shot Injection Molding: Allows for the injection of multiple materials or colors in a single mold cycle, enabling over-molding and producing complex parts.
- Gas-Assisted Injection Molding: Uses pressurized gas to hollow out sections of the part, reducing material usage and eliminating sink marks.
- Insert Molding: Involves encapsulating pre-inserted components (such as metal inserts) with molten plastic to create a single integrated part.
- Reaction Injection Molding (RIM): Combines two reactive components to form a thermosetting polymer, suitable for producing components with high strength and durability.
Materials Used in Injection Molding :
- Polyethylene (PE): Offers excellent chemical resistance and is widely used for packaging and consumer goods.
- Polypropylene (PP): Known for its lightweight, durability, and heat resistance, used in various applications, including automotive parts and medical devices.
- Polyvinyl Chloride (PVC): Used in a variety of products, including pipes, cables, and medical equipment.
- Polystyrene (PS): Commonly used for packaging materials, food containers, and consumer goods.
- Acrylonitrile Butadiene Styrene (ABS): Offers a balance of strength, impact resistance, and cost-effectiveness, commonly used in automotive parts and electronics.
- Polyethylene Terephthalate (PET): Widely used for beverage bottles, packaging, and textile fibers.
- Polyamide (Nylon): Known for its high strength, heat resistance, and wear resistance, used in automotive and industrial applications.
- Polycarbonate (PC): Offers excellent impact resistance and optical clarity, used in eyewear, automotive, and electronics.
- Polyurethane (PU): Used in reaction injection molding (RIM) to produce parts with high strength and flexibility, commonly found in automotive components and medical devices.
Injection Molding Equipment :
- Clamping Unit: Responsible for closing and holding the mold halves together under high pressure during the injection and cooling process.
- Injection Unit: Comprises the barrel, screw, and nozzle, where the plastic pellets are heated, melted, and injected into the mold cavity.
- Mold: The core component, consisting of two halves, defines the shape of the part and provides channels for plastic flow and cooling.
- Ejector System: Utilizes ejector pins or ejector plates to remove the finished part from the mold after cooling.
- Hydraulic or Electric System: Provides the necessary power and control for the various machine movements, such as clamping, injection, and ejection.
Injection Molding Trends and Future Outlook :
- Advanced Materials: Development of new and high-performance materials with enhanced properties, such as biodegradable and bio-based polymers.
- Industry 4.0 Integration: Adoption of Industry 4.0 principles, including IoT, data analytics, and automation, for smart and connected injection molding processes.
- Micro Injection Molding: Growing demand for miniaturized products in electronics and medical devices is driving advancements in micro injection molding technology.
- Sustainable Solutions: Increased focus on eco-friendly practices, with an emphasis on recyclable and biodegradable materials, as well as energy-efficient processes.
- Additive Manufacturing Integration: The integration of 3D printing with injection molding for creating molds and inserts, reducing lead times and costs.
- Smart Tools and Sensors: Utilizing intelligent molds with sensors to monitor temperature, pressure, and part quality in real-time for process optimization.
- Customization and Personalization: Advancements in tooling technology allow for the cost-effective production of customized parts, catering to individual customer needs.
- Virtual Prototyping and Simulation: The use of virtual prototyping and simulation software for faster design validation and optimization, reducing time to market.
The injection molding industry is continually evolving, driven by advancements in technology, materials, and sustainability initiatives. Key trends and future outlook for injection molding.
Advantages of Injection Molding :
- High Efficiency and Production Speed: Injection molding allows for rapid production of parts in large volumes, ensuring cost-effectiveness for mass production.
- Precision and Complexity: The process enables the production of intricate and complex parts with high dimensional accuracy and consistency.
- Material Versatility: A wide range of materials can be used, each offering specific properties suitable for different applications.
- Minimal Material Waste: The ability to control material usage reduces waste, making injection molding environmentally friendly.
- Consistent Quality: Injection molding provides consistent part quality, reducing variability and improving overall product performance.
- Automation and Labor Savings: Injection molding machines can be highly automated, reducing the need for manual labor and enhancing production efficiency.
- Cost-Effectiveness: Efficiency, repeatability, and material optimization contribute to cost-effective production.
- Wide Range of Applications: Injection molding is suitable for producing parts in various industries, from automotive and electronics to medical and consumer goods.
How Shivay Enterprise is different from other Injection Molding companies:
- Advanced Technology:Â Shivay Enterprise utilizes state-of-the-art injection molding machines and cutting-edge technology to ensure precise and efficient production processes.
- Expert Team: With a team of highly skilled professionals, Shivay Enterprise offers extensive expertise in injection molding, capable of handling complex projects with precision.
- Material Versatility:Â Shivay Enterprise works with a wide range of thermoplastic and thermosetting materials, catering to diverse industry needs and applications.
- Customization: Understanding each client’s unique requirements, Shivay Enterprise provides tailored solutions and adapts its processes accordingly.
- Quality Assurance:Â Shivay Enterprise maintains stringent quality control measures throughout the production process, delivering flawless and high-performance components.
- Comprehensive Services: From design support to post-processing, Shivay Enterprise offers comprehensive in-house capabilities, streamlining the entire manufacturing process.
- Cost-Effectiveness: Despite its commitment to excellence, Shivay Enterprise optimizes processes to provide cost-effective injection molding solutions.
Injection Molding is used in a wide variety of applications, including:
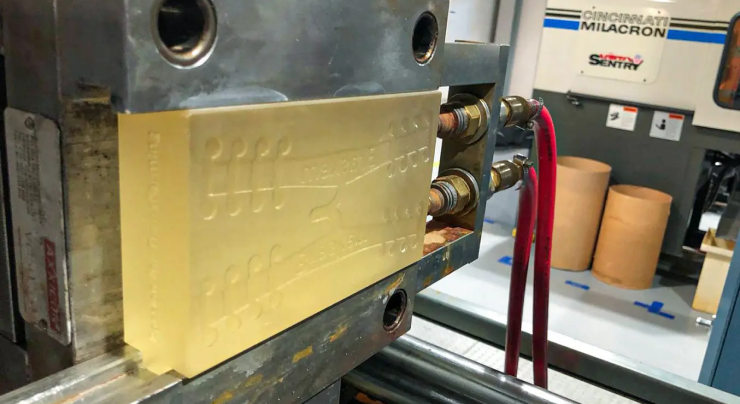

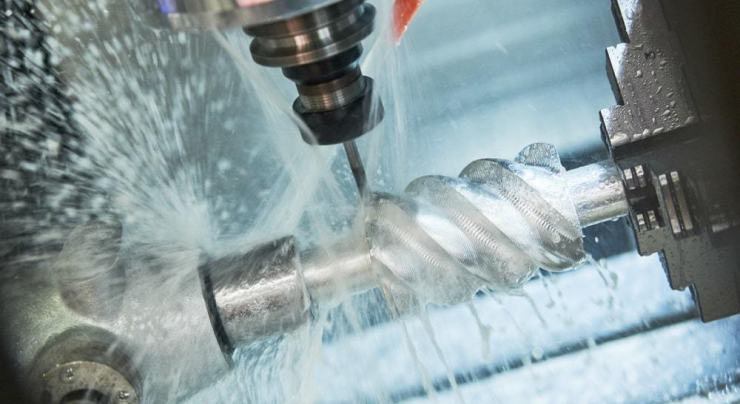
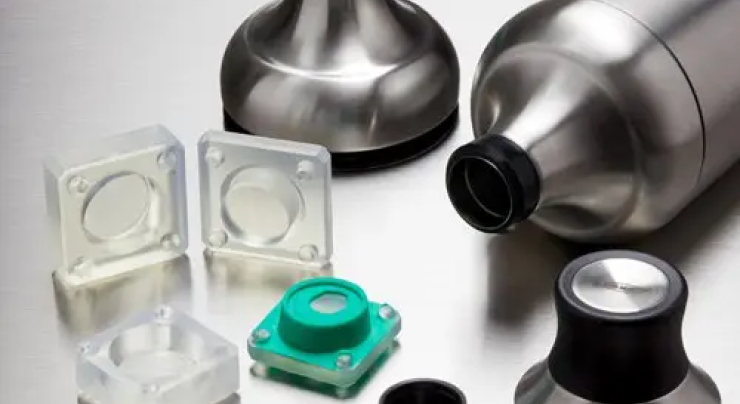
- Automotive: From interior components and dashboard parts to engine and transmission components.
- Electronics: Producing casings, connectors, and housings for electronic devices.
- Packaging: Manufacturing bottles, containers, and caps for the food and beverage industry.
- Medical Devices: Producing intricate and sterile components for medical equipment and devices.
- Consumer Goods: Manufacturing a variety of consumer products, including toys, kitchenware, and household items.
- Aerospace: Producing lightweight and durable components for aircraft and aerospace applications.
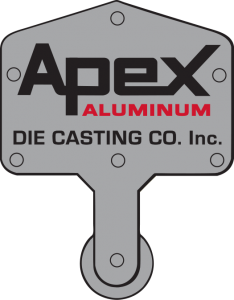
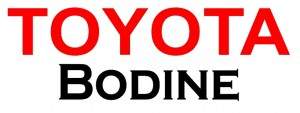
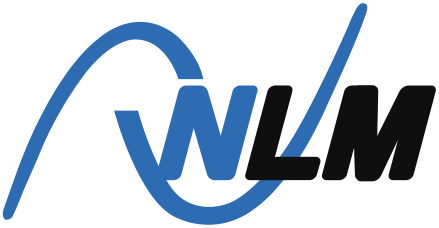

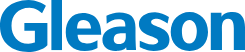
How Shivay Enterprise can help you with Injection Molding servicing:
- Expertise and Experience:Â Shivay Enterprise boasts a team of skilled professionals with extensive expertise in pressure die casting. With years of experience, they can handle complex projects efficiently and deliver high-quality results.
- State-of-the-Art Facilities: Equipped with advanced CNC machines and modern casting technology, Shivay Enterprise ensures precise and consistent pressure die-casting processes.
- Material Selection:Â Shivay Enterprise offers versatility in material selection, working with a wide range of alloys, including aluminum, zinc, copper, and magnesium, to meet specific application needs.
- Customized Solutions: Understanding that each project is unique, Shivay Enterprise provides tailored solutions to match clients’ requirements, ensuring optimal casting results.
- Quality Control: Committed to delivering flawless components, Shivay Enterprise implements rigorous quality control measures throughout the casting process, ensuring consistent and reliable outcomes.
- Global Reach: Shivay Enterprise serves clients worldwide, establishing a reputation for reliability and trust in international markets.