Casting
Where Quality Meets Efficiency: Shivay Enterprise’s Casting Expertise in the CNC Industry
Casting Services :
What is Pressure Die Casting ?
Pressure die casting is a highly versatile and widely used manufacturing process for producing complex and precise metal components. It is a form of permanent mold casting that involves injecting molten metal under high pressure into a reusable mold cavity, called a die. The process offers several advantages, including high production rates, excellent dimensional accuracy, and the ability to produce intricate shapes with minimal post-processing.
The origins of pressure die casting can be traced back to the mid-19th century when the process was first patented in the United States and Europe. Initially, the process was used to cast simple lead and tin alloys. However, with advancements in technology and materials, pressure die casting evolved into a reliable and widely used method for producing various metal components.
During World War II, pressure die casting gained prominence as it played a crucial role in producing military equipment and components. After the war, the process expanded into different industries, including automotive, aerospace, electronics, and consumer goods, where its advantages were highly valued.
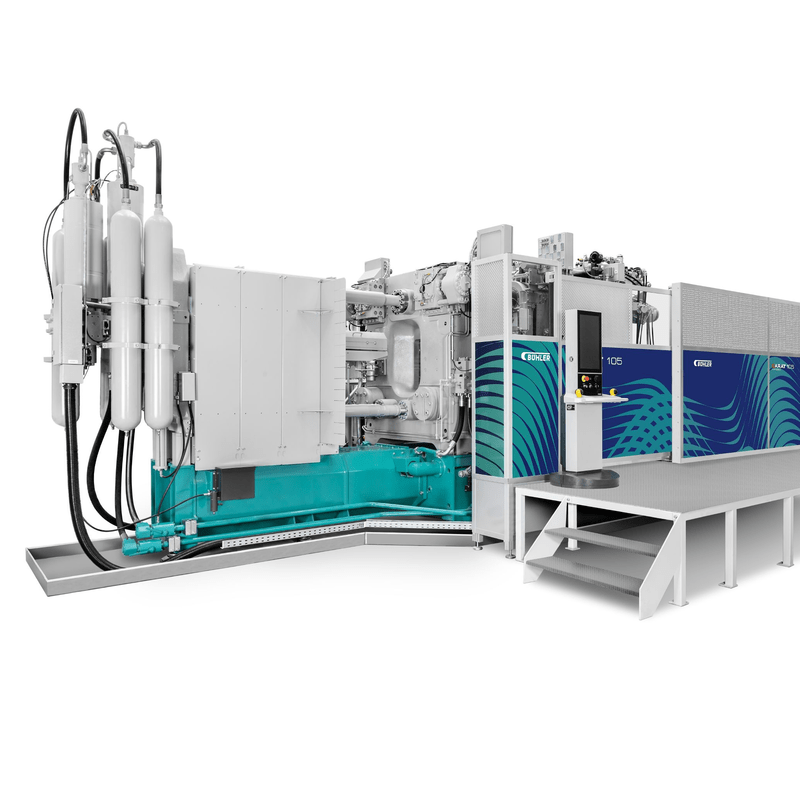
Pressure die casting is a metal casting process that is used to create intricate metal parts with high precision. In pressure die casting, molten metal is injected into a mold under high pressure. This forces the metal to fill all of the details of the mold, creating a part with a smooth, uniform surface finish.
Types of pressure die casting :
1. Hot Chamber Die Casting:
Hot chamber die casting, also known as gooseneck casting, is a process primarily used for casting low-melting-point alloys, such as zinc, tin, and lead-based alloys. The key characteristic of hot chamber die casting is that the injection mechanism is submerged in the molten metal, reducing the need for a separate melting furnace.
Advantages:
- Faster cycle times due to the immediate availability of molten metal in the shot chamber.
- Ideal for producing small to medium-sized parts with excellent surface finish and dimensional accuracy.
- Less material wastage as the system is self-contained and uses only the necessary amount of molten metal for each casting.
2. Cold Chamber Die Casting:
Cold chamber die casting is suitable for casting high-melting-point alloys, such as aluminum, magnesium, and copper-based alloys. In this method, the injection system is external to the molten metal holding furnace, making it more suitable for casting metals with higher melting temperatures.
Advantages:
- Suited for casting higher melting point alloys, including aluminum, which is widely used in various industries.
- Ideal for producing larger and more complex components.
- Allows for precise control of the casting process, making it suitable for critical applications.
3. Gravity Die Casting::
Gravity die casting, or permanent mold casting relies on gravity to fill molds with molten metal. It offers controlled casting for precise components with smooth surfaces and dimensional accuracy in various industries.
Advantages:
- Excellent Surface Finish: Gravity die casting yields parts with superior surface finish, reducing the need for extensive post-processing.
- Dimensional Accuracy: Tight tolerances and high dimensional accuracy ensure consistent part quality.
- Cost-Effective for Medium to High Volumes: Ideal for cost-effective medium to high-volume production runs.
Materials Used in Pressure Die Casting:
- Aluminum: Aluminum and its alloys, such as A380, A383, and ADC12, are the most popular materials for pressure die casting due to their excellent castability, lightweight, and good mechanical properties.
- Zinc: Zinc alloys, like Zamak 3, Zamak 5, and ZA-8, are commonly used for applications requiring intricate details and thin walls. Zinc has good fluidity, high impact strength, and is cost-effective.
- Magnesium: Magnesium alloys are lightweight and offer excellent strength-to-weight ratios, making them suitable for applications in the aerospace and automotive industries.
- Copper: Copper-based alloys are used for specialized applications that require high electrical and thermal conductivity.
- Brass: Brass, a combination of copper and zinc, is used for parts that require both strength and corrosion resistance.
- Lead and Tin: Lead and tin alloys are used for specific applications in industries such as plumbing and electronics.



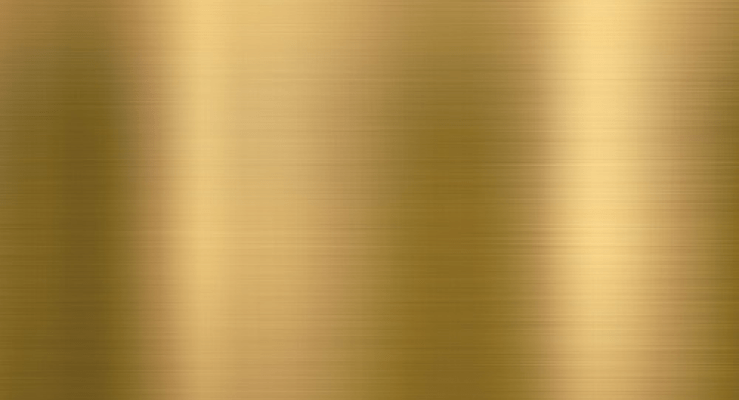
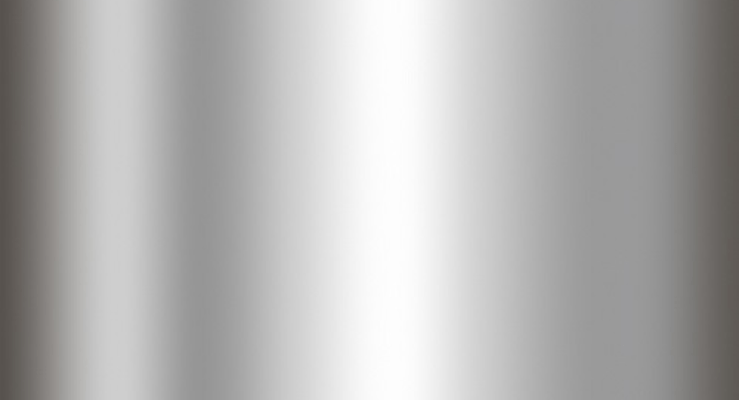

Process of Pressure Die Casting :
- Mold Preparation: A metal mold, usually made of steel or other durable materials, is prepared. The mold consists of two halves, an ejector half and a cover half, that fit together to form the mold cavity.
- Preheating: The mold is preheated to a specific temperature to improve the flow and solidification of the molten metal.
- Injection: Molten metal is injected into the mold cavity at high pressure using a hydraulic or mechanical press. The pressure ensures that the molten metal fills all the intricate details of the mold.
- Cooling and Solidification: Once the mold cavity is filled, the molten metal is allowed to cool and solidify to form the desired shape.
- Ejection: After the metal solidifies, the two halves of the mold are separated, and the finished part, known as the casting, is ejected from the mold.
- Trimming and Finishing: The casting may undergo post-processing steps, such as trimming excess material, removing any surface imperfections, and applying surface treatments like painting or plating.
Future of Pressure Die Casting :
1. Advanced Materials: Manufacturers are exploring the use of new and advanced materials, such as high-performance alloys and composites, to enhance the mechanical properties and performance of pressure die-cast components. These materials offer benefits like increased strength, lightweight, and improved corrosion resistance.
2. Additive Manufacturing Integration: The integration of additive manufacturing techniques, like 3D printing, with pressure die casting, is gaining attention. This hybrid approach allows for the creation of complex cores, inserts, and cooling channels in the die, leading to improved part quality and reduced production lead times.
3. Simulation and Modeling: The adoption of advanced simulation and modeling software allows for more accurate predictions of the die-casting process, optimizing design, and material usage, and reducing defects in the castings. Virtual simulations help identify potential issues before the actual casting process takes place, leading to cost savings and process improvements.
4. Industry 4.0 and Smart Manufacturing: Pressure die casting foundries are embracing industry 4.0 principles and smart manufacturing practices. The use of sensors, IoT devices, and real-time data analytics allows for continuous monitoring and optimization of the casting process, leading to increased efficiency, reduced downtime, and improved quality.
5. Sustainable Practices: Environmental concerns are driving the adoption of more sustainable practices in the pressure die-casting industry. Efforts are being made to reduce energy consumption, optimize material usage, and implement recycling and waste reduction initiatives.
6. Miniaturization and Micro Die Casting: The demand for miniaturized and precise components in various industries, such as electronics and medical devices, is driving the development of micro die-casting techniques. Miniature die casting offers the ability to produce intricate small-scale components with high accuracy.
7. Customization and Personalization: Customers’ increasing demand for customized products is influencing the pressure die-casting industry. Manufacturers are working towards providing more flexible and responsive production capabilities to cater to individual customer needs.
8. Improved Casting Technology: Ongoing research and development efforts are focused on enhancing the casting process itself. This includes advancements in injection systems, die coatings, and vacuum-assisted die casting, leading to improved surface finish, reduced porosity, and enhanced overall part quality.
As the industry embraces innovation and automation, pressure die casting will continue to be a vital manufacturing process, serving a wide range of industries and applications with high-quality, complex, and precise metal components.
Advantages of Pressure Die Casting
- High Production Rates: Pressure die casting allows for high production volumes, making it a cost-effective choice for mass production.
- Excellent Dimensional Accuracy: The process provides tight tolerances and precise dimensional accuracy, ensuring consistent quality across batches.
- Complex Geometries: Pressure die casting can produce intricate and complex shapes with fine details that are difficult to achieve using other manufacturing processes.
- Minimal Post-Processing: The casting produced by pressure die casting typically requires little to no post-processing, reducing production time and costs.
- Thin-Wall Casting: The process is capable of producing thin-walled components, making it suitable for lightweight applications.
- Smooth Surface Finish: Pressure die casting produces parts with smooth surface finishes, reducing the need for additional finishing operations.
- Reduced Material Waste: The process has minimal material wastage as the excess metal can be recycled and reused.
How Shivay Enterprise is different from other Sheet metal fabrication companies:
- Extensive Expertise: Highly skilled and experienced professionals with deep expertise in pressure die casting.
- State-of-the-Art Technology: Equipped with cutting-edge CNC machines and advanced casting technology for unmatched accuracy.
- Customization and Flexibility: Focus on understanding and catering to each client’s unique needs with customized solutions.
- Range of Materials: Versatility in working with various materials, catering to diverse industries and applications.
- Quality Assurance: Stringent quality control measures ensure flawless and high-performance components.
- In-House Capabilities: Comprehensive in-house facilities, from mold design to finishing and assembly, streamline production.
- Innovation and Continuous Improvement: Constant investment in research and development to stay at the forefront of industry innovations.
- On-Time Delivery: Prioritization of meeting project timelines for seamless integration into clients’ manufacturing processes.
- Cost-Effectiveness: Offering competitive pricing without compromising on quality through process optimization.
- Customer-Centric Approach: Open communication, attentive support, and active collaboration to prioritize client satisfaction.
- Diverse Industry Experience: Proven track record in serving various industries, demonstrating adaptability.
- Global Reach: Catering to clients worldwide, building strong relationships and trust across international markets.




Pressure Die Casting is used in a wide variety of applications, including:
- Automotive: Used for producing engine components, transmission parts, housings, and other automotive parts.
- Aerospace: Components for aircraft engines, structural parts, and aircraft interiors are often manufactured using pressure die casting.
- Electronics: Used for producing electronic enclosures, connectors, and other electronic components.
- Consumer Goods: Pressure die casting is used to produce items such as kitchenware, lighting fixtures, and hardware.
- Telecommunications: Components for telecommunication devices and equipment are commonly manufactured using pressure die casting.
- Industrial Machinery: Used in the production of various industrial equipment and machinery parts.
- Medical Devices: Some medical equipment and devices are manufactured using pressure die casting.

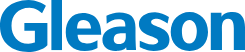



How Shivay Enterprise can help you with Pressure Die Casting servicing:
- Expertise and Experience: Shivay Enterprise boasts a team of skilled professionals with extensive expertise in pressure die casting. With years of experience, they can handle complex projects efficiently and deliver high-quality results.
- State-of-the-Art Facilities: Equipped with advanced CNC machines and modern casting technology, Shivay Enterprise ensures precise and consistent pressure die-casting processes.
- Material Selection: Shivay Enterprise offers versatility in material selection, working with a wide range of alloys, including aluminum, zinc, copper, and magnesium, to meet specific application needs.
- Customized Solutions: Understanding that each project is unique, Shivay Enterprise provides tailored solutions to match clients’ requirements, ensuring optimal casting results.
- Quality Control: Committed to delivering flawless components, Shivay Enterprise implements rigorous quality control measures throughout the casting process, ensuring consistent and reliable outcomes.
- Global Reach: Shivay Enterprise serves clients worldwide, establishing a reputation for reliability and trust in international markets.